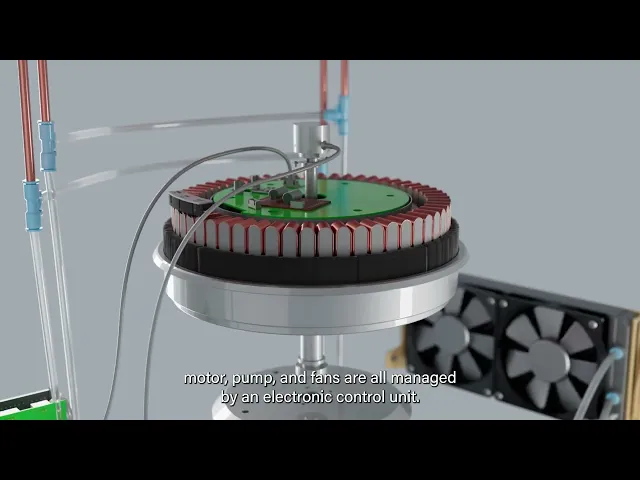

Forget refrigerants, we don't need them.
Scroll to learn how we use magnetocaloric materials.
Material
Instead of refrigerant gasses our cooling cycle uses solid-state magnetocaloric materials, which heat up when magnetised and cool down when demagnetised. We use Lanthanum-Iron-Silicon (LaFeSi) alloys which are developed for scaling, using only abundant elements, with optimisation for production and in-device performance.
Coating
To prevent corrosion of our iron based materials, we apply a supplementary metal coating to the exterior. Our novel method stabilises the material for long term use and is a milestone innovation which lays the groundwork for the commercialisation of magnetic cooling.
Active Magnetocaloric Regenerator (AMR) Module
We extract the power of our material through Active Magnetic Regeneration (AMR). A cyclic process which synchronises material temperature change with the flow of a transfer medium to create usable temperature spans. The AMR module houses this process, managing the transfer medium flow and distributing to the wider system.
Transfer Medium
In room temperature applications, we separate hot and cold in the AMR module using a transfer medium comprising of water and alcohol to prevent freezing. A hydraulic system regulates this flow at atmospheric pressure through the porous structure of the material and on to either a radiator for heat expulsion or an end application to harness the cooling effect.
Magnetisation
We use permanent magnets to generate a magnetic field in our room temperature systems. Exposing this magnetic field to our AMR module causes the material to heat up. The transfer medium then flows through the porous material and absorbs the heat, which is carried to a radiator to dissipate.
Demagnetisation
Demagnetising the AMR module allows the material to cool. Thermal energy present in a new flow of the transfer medium is then absorbed by the material, thus cooling it. The now cold transfer medium is then directed to the end application to provide the cooling effect.
Sourcing and Circularity
Our permanent magnets will continue to work indefinitely, making them ideal for reuse in future systems and beyond. With a cradle to cradle approach, we are exploring magnet sourcing from decommission in other applications, while also continually reviewing the potential of alternate field generators.
How is this process more efficient?
Magnetic forces are inherently efficient as they waste no energy through heat. Balancing our magnetic processes in rotational sequence also allows the recovery of work, increasing cycle efficiency by up to 30% against alternatives.
Engineering Approach
Our innovation doesn’t end with magnetocalorics. To build commercially viable systems, we optimise our technology for cost, efficiency and longevity, engineering novel solutions across a network of components. Alongside broad internal expertise, we work closely with key industry partners to bring magnetic cooling to life.
The future’s looking cool
We’ve nurtured magnetic cooling technology from research paper, through lab set up and into market with our POLARIS and ECLIPSE platforms. With development of platforms at 5kW, 15kW and beyond, our portfolio is constantly expanding, making magnetic cooling available across even more application areas. Through the Hylical project, we’re also actively developing a platform for hydrogen liquefaction, read more about it on the Hylical website.
Get in touch with our team.
Company
Tech
Contacts
Legal
© 2025 MAGNOTHERM Solutions GmbH. All Rights Reserved.